Motorized Gantry Cradle
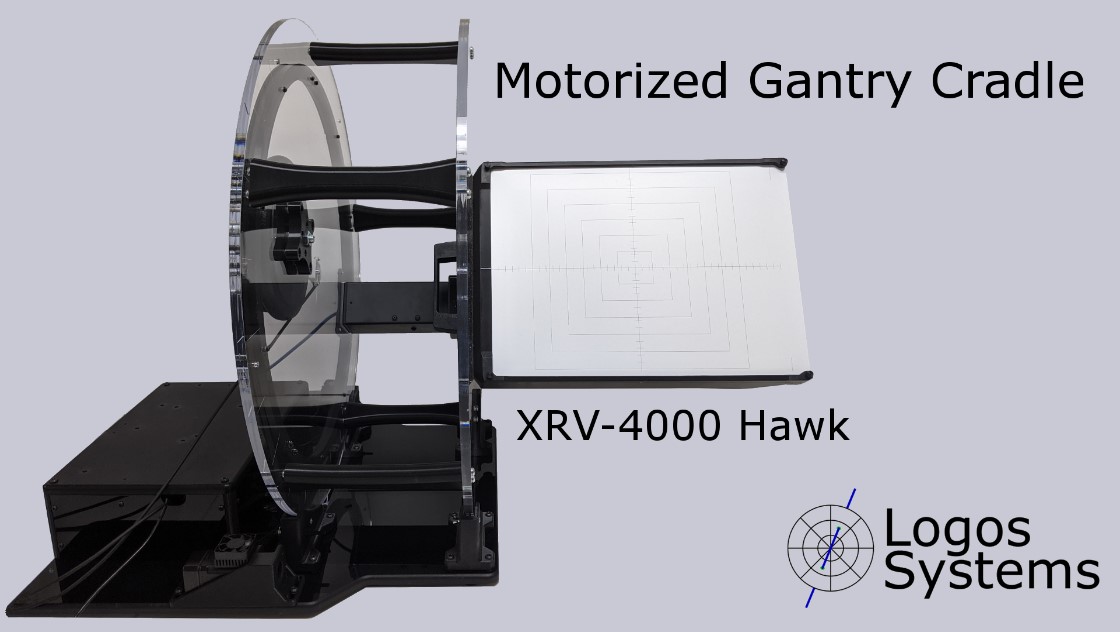
The Motorized Gantry Cradle option for the XRV-2000 Falcon, XRV-3000 Eagle, and XRV-4000 Hawk enables 0 – 360 degree measurements on fields up to 320x420 mm. Using advanced tracking algorithms and two inclinometers, the Motorized Gantry Cradle takes automated beam measurements continuously as the gantry moves. Because of the reduced time needed for human interaction, QA becomes faster and more efficient.
Coupled with the XRV-2000 Falcon, XRV-3000 Eagle, or XRV-4000 Hawk, the Motorized Gantry Cradle can be set to automatically follow a moving gantry, stop for the delivery, and continue to move with the gantry to the next desired gantry angle. The gantry inclinometer quickly attaches with a removable suction cup. Angle data is read from the inclinometers and is included in the output data. Gantry versus cradle angle following accuracy is typically within 0.5 degrees.
All operations are controlled by a laptop PC supplied with the Motorized Gantry Cradle and XRV detector phantom. The XRV comes with a 30 meter (100 feet) USB3 power-over-fiber extender cable so that the system PC and operator can be located safely away from the radiation source. The Motorized Gantry Cradle comes with a separate CAT6 based USB 2.0 extender for the Motor Controller and two inclinometers. A handheld digital level is provided with the Gantry Cradle system to cross-reference with the 2 integrated inclinometers.
Features and Benefits:
- Proton and X-ray beam profiling over 360° rotation
- Automatic Gantry Following modes reduce QA time and room entry
- Support for XRV-2000 Falcon, XRV-3000 Eagle, and XRV-4000 Hawk
- Remote control via 30m CAT6 cable from laptop
- Motion control plan scripting
- Gantry angle data integrated with beam measurements
- Fluence volume reconstruction for 10 x 10 x 15cm volume*
- XY multi-beam spot analysis at any gantry angle
- Proton range verification at any angle using a Ranger or LCW
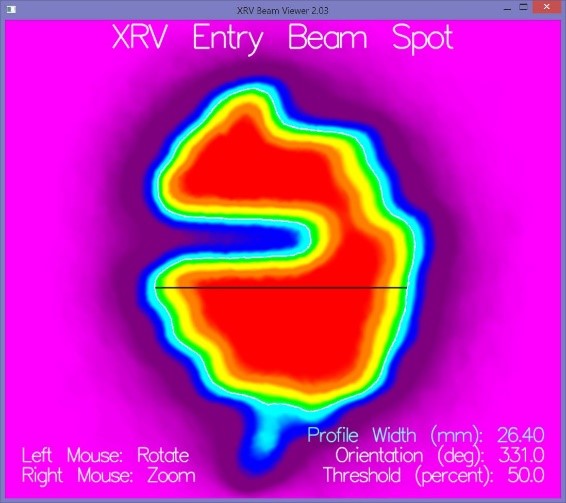
Motorized Gantry Cradle Operation
After the Falcon, Eagle, or Hawk phantom is assembled in the Motorized Gantry Cradle, it may be CT scanned to allow targeting of the embedded fiducials in the treatment planning software. The Gantry Cradle can be turned manually if scanning at alternate angles is needed.
In the treatment room, the Phantom is placed on the treatment couch so the room lasers align the scintillator to the gantry isocenter. The Gantry Inclinometer is attached to the Gantry using the included suction cup. Before delivery of the QA treatment plan, several Logos software applications must be running: BeamWorks Angle Server, BeamWorks Gantry Cradle Control, and BeamWorks Strata. For higher Gantry speeds (> 1 deg/sec) check the “enhanced” button on BeamWorks Angle Server.
Home the Gantry Cradle, then enable Adaptive Follow Mode using the multifunction button on the right of BeamWorks Gantry Cradle Control. When the Start button is clicked, the phantom will align itself with the Gantry. In BeamWorks Strata, select the desired capture script and click Start Script. During the plan execution, the phantom will follow the Gantry around as the QA delivery proceeds. Angle data is captured in WinLVS at the same time as the beam data and is embedded into the measurements taken during delivery. Click Stop Script to complete the data capture.
Analysis of the captured data may be done using the included programs: BeamWorks Strata, Profile View, and WinLVS. Spot position, size, profile, and duration can be measured using these included programs. Measurements can be exported directly into an Excel template to perform trend analysis. Data is exported in formats that can be analyzed using third-party software programs such as MATLAB, Python, Excel or ImageJ. Fluence reconstruction can be performed in the VolumeWorksXL software for a 3D view of the delivery.
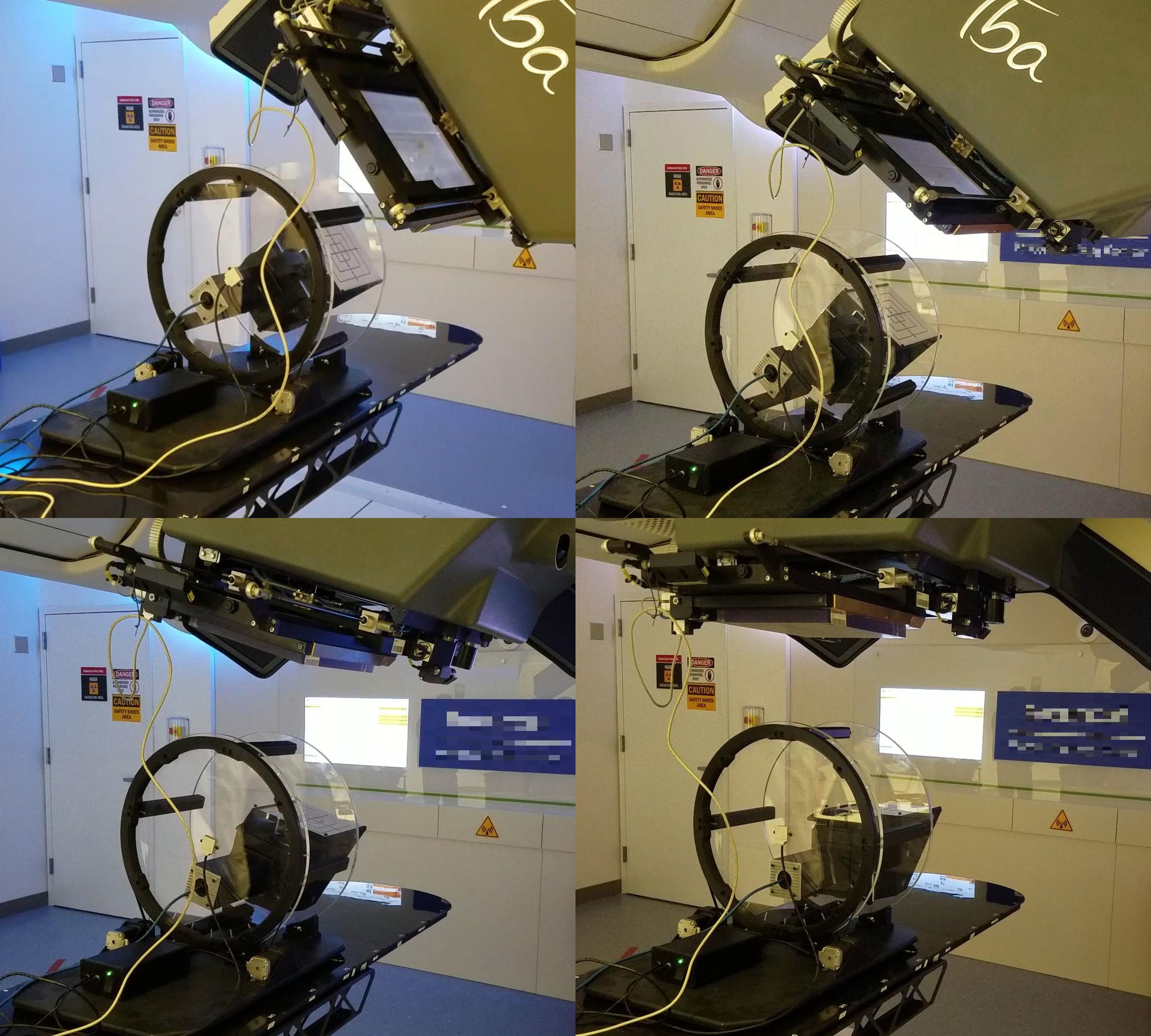
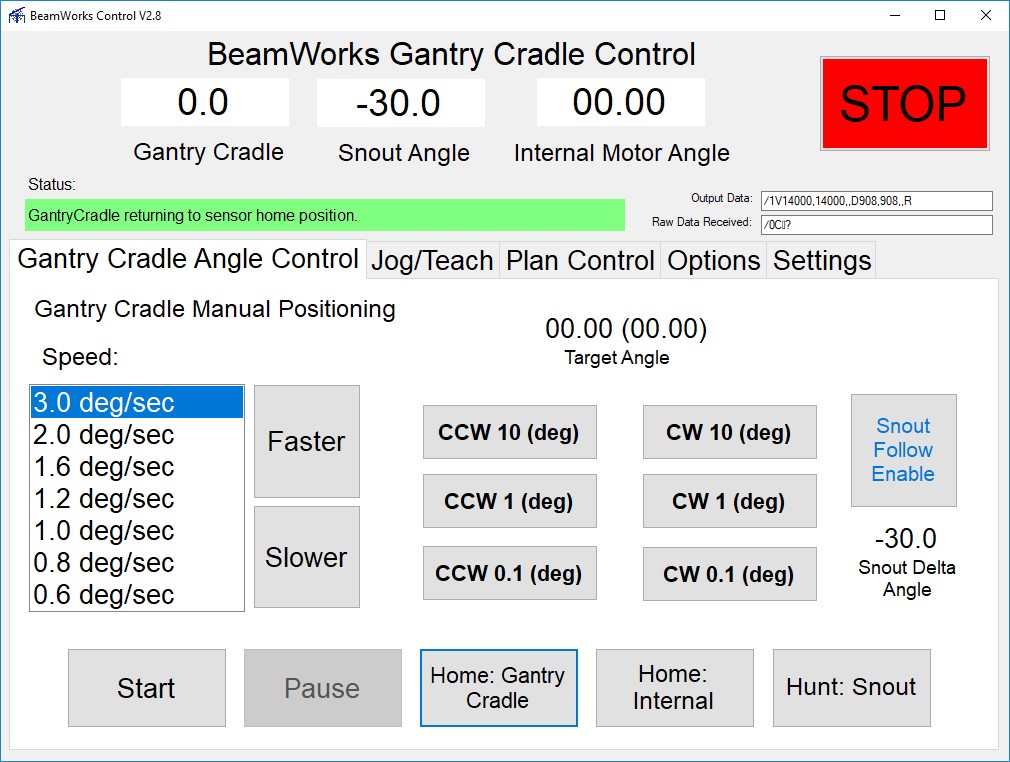
Motorized Gantry Cradle Specifications:
Runout: | Max. ± 1mm over 360 degrees |
---|---|
Angular Precision: | 0.1 degrees(typical) |
Deviation from Gantry: | 0.2-0.5 degrees (typical) |
Angle Period: | 250 ms between acquisitions |
Interface: | CAT6 USB 2.0 Extender |
XY Beam Center: | 0.22 - 0.3 mm |
---|---|
Repeatability: | ± 0.04 mm (typical) |
Beam Diamter: | 0.1 mm |
Repeatability: | ± 0.04 mm (typical) |
Resolution: | 1280x960-1200x1600 pixels, 8 or 12-bits per pixel |
---|---|
Capture Rate: | 1 - 30 frames/sec (max) |
Scintillator Size: | 200 × 200 mm - 320 × 420 mm |
Camera Interface: | USB 3.0, fiber optic extender |
Camera top and sides: | 15 mm bismuth composite |
---|---|
CCD Lifetime: | ~1,500 beam hours |
Capture Trigger: | Auto, GUI, Script, or Network watch-file |
---|
Electrical Power: | 110-220V or battery |
---|---|
Environment: | 5 to 30 degrees C; 90% humidity, no condensation; minimal vibration |
Notes:
- Resolution accuracy dependent on phantom: 0.22 mm (1280x960) for Falcon, 0.3 mm (1200x1200) for Eagle, and 0.3mm (1200x1600) for Hawk. Max capture rate for the Eagle and Hawk is 15 frames/sec.
- Contact us for custom shielding requirements. The camera may be replaced for a service fee after approximately 3 years as necessary.
- Contact us for custom camera requirements. Higher resolution and higher frame rates are both possible.